
Stewardship: We conduct our business in a manner that is reflective and protective of the public trust in us as stewards of the University’s facilities.
Part of the Values at Work Series
Building a Legacy: One Piece at a Time
The Overview
This article provides an overview of The University of Texas at Austin’s journey to build and implement a world-class strategy for its comprehensive preventive maintenance program that will move the program forward well into the future. Subsequent articles will follow to provide a more detailed look at the implementation of this major initiative.
“It’s not only what we do now that matters; it’s the path we’ve established for the next generation that will be our legacy,” states Darnell Mack, an electrical engineer and project manager with Facilities Operations & Maintenance (FOM), a division of the Facilities Services department at the university. This is her vision, but she is not alone.
Is she talking about the environment? Education? Trust funds? What she is talking about is being a steward of the facilities at The University of Texas at Austin.
For nearly 30 years Mack has served in the realm of facilities, providing engineering, project management, and quality control services in the manufacturing and heavy commercial industries. Her passion these days is her work on the Maintenance Improvement Initiative, or MI2. This initiative is a core strategy for FOM. What does MI2 mean to the university?
“It is really about a fundamental change to the way we have historically looked at and managed maintenance,” explains Dan Clairmont, associate director for FOM. “Performing routine, preventive maintenance (PM) in campus facilities is intended to maximize the useful life, reliability, and efficiency of building systems. However, it is expensive. As good stewards of the university’s resources, it is critical for us to validate that it is performed in the most efficient manner and results in value-added benefits.”
“IT IS REALLY ABOUT A FUNDAMENTAL CHANGE TO THE WAY WE HAVE HISTORICALLY LOOKED AT AND MANAGED MAINTENANCE.”
To accomplish this, Clairmont has made MI2 the division’s number one strategic priority. They are breaking down every aspect of their existing maintenance program to the most basic levels and rebuilding it. This is an enormous task, but an essential step in their journey toward becoming a truly world-class maintenance organization—what you would expect at The University of Texas at Austin.
FOM currently maintains over 60,000 individual pieces of equipment and devotes around 60 percent of its available worker-hours each year to performing preventive/scheduled maintenance of that equipment—approximately $6 million per year in direct labor costs alone. Managing this effort is a huge task. Ensuring it is managed efficiently and delivers measurable results was a clear objective of MI2. However, there was something more they needed to accomplish with the initiative. They needed to tell their story.

Technician changes filters on air handler unit.
Even before they began developing MI2, FOM’s hypothesis was that the division was under-resourced to provide world-class maintenance. They knew they were not doing all the maintenance they should do. The questions were, “What would it take to do all the maintenance they should do, and what is the risk to the university’s mission?” University leaders would need this information to determine if they could accept that risk. However, before asking leaders to make that decision, FOM would need to show that the division is addressing the highest priority requirements and effectively utilizing their existing resources. This was the story MI2 needed help to tell, but telling the story would require a major overhaul to FOM business processes. Here is how they did it:
1. What resources do you think you need?
Prior to implementing MI2, FOM managers did not know what resources they needed. Business processes were not set up to allow them to determine reliably which maintenance items were currently not being accomplished much less quantify the requirements for enhancing the maintenance program. This had to be step one.
What Is Not Getting Done? Step one began with implementing a business process that would help FOM distinguish between PM work orders that were successfully performed and those that were not completed due to a lack of resources. Previously, all PM work orders were closed, whether they were completed or not. The only distinction between a completed work order and a skipped work order was that skipped work orders had no hours charged. This was a relatively simple fix. Instead of closing skipped work orders, FOM cancelled them. The next obvious question was “Why was it cancelled?” To answer that, they configured their computerized maintenance management system (CMMS) to categorize the reason for cancelling a PM work order. They can now clearly identify the PM work orders cancelled due to a lack of resources, or for other reasons. They can also easily and reliably show the completion percentage for PM work orders and have confidence that a closed PM work order was actually done. Now able to identify the PM work orders that were cancelled due to a lack of resources, the next step for FOM was to determine the number of labor hours by trade required to complete the cancelled work.
How Many Hours Do You Need? FOM found that the estimated labor hours to perform each PM work order, if recorded at all, were not accurate. Thus, FOM could not accurately predict how many specific craftsmen, such as plumbers or mechanics, were needed to perform the PMs.
To provide a means for estimating the needed resources, they are mapping the PMs to the equipment to be maintained. They are breaking down the PMs and indexing them by class of equipment, maintenance objective, and the tasks involved, as shown below:
Class of equipment – Such as a fan or pump Objective – Which PMs should be done to best prevent failure? Tasks – What needs to be done to carry out the objective? Examples include lubricate the bearing and perform a visual inspection
The steps vary, based on specific equipment details, but the objective(s) should remain the same. This analysis provides a strong basis for estimating hours needed to complete the PMs. FOM is currently in the stage of identifying objectives. Drilling down to the details is still on the table for this team in order to make the full-scale improvements they want to make. Yet, a strong maintenance team knows that while estimating the hours needed is important, the long-term value to accurate estimates is to help manage the program by comparing estimated with actual hours and providing the ability to project resource requirements.
Align actual hours with estimates. Evaluating estimated hours and developing metrics ensures that the actual hours align with the estimates. “When you have confidence that the estimated hours are accurate, you will also be able to compare them to the actual hours charged to give an indicator that the work is being done efficiently and completely,” Mack explains. The managers can spot the outliers and then research the reason for the discrepancy, which they can document for future reference.
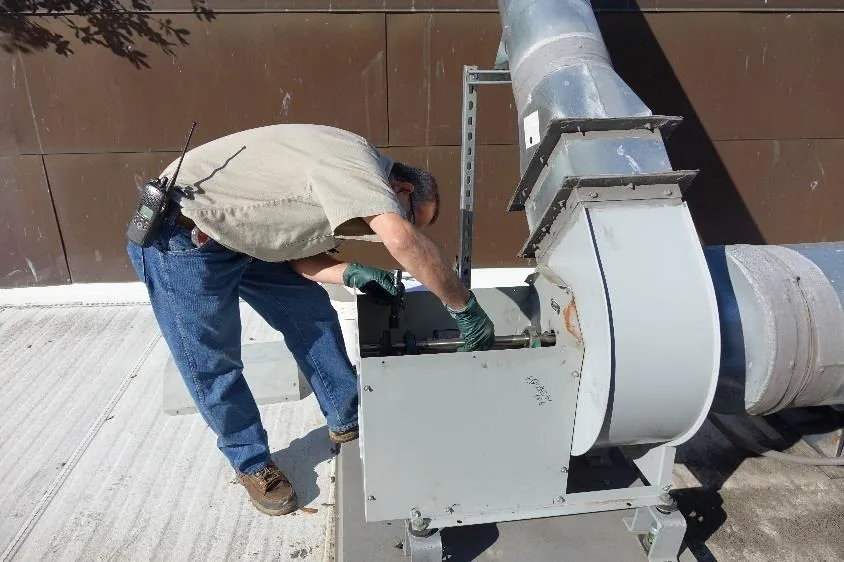
Technician inspects rooftop fan at the Union Building.
When the actual and estimated hours are closely aligned, this is an indicator that the job was done properly. Mack states, “Our focus has to be on the quality of the work to ensure our buildings and equipment operate safely and efficiently. Our goal is to stress to our technicians that the quality of work is most important, not the quantity.” With clearly written instructions and the expected amount of time required to do the work, technicians have the freedom to do the job right the first time without the stress of being told to work faster, which ultimately has a negative impact on quality.
2. How can you prove you are effectively using the resources you have?
According to the MI2 team, there were two imperatives to ensure FOM was effectively applying its resources to the most critical maintenance items: setting priorities for the PMs and implementing a process to schedule individual technicians for specific work orders.
Set priorities. Before MI2, all PM tasks were assigned the same priority. If there were over 1,000 work orders for a week, there was no way to prioritize those work orders. FOM now categorizes PMs based on four priorities and has established clear completion goals for each priority (Table 1). Unlike client requested work, known in FOM as Trouble Calls, where priorities drive a certain response time, PM priorities drive a completion rate. Clairmont explains, “It does not matter, within reason, how quickly we accomplish a priority 1 PM; it matters that it is completed in a quality manner.” This allows employees to work on the most important tasks first. Then, they proceed with lower priority requirements until they run out of available hours to complete them. PREVENTIVE MAINTENANCE |
PREVENTIVE MAINTENANCE | ||||
Priority | Description | Comments | Examples | Goal/Band |
1 |
LIFE SAFETY / CODE |
Life safety or code required PMs. |
|
98% - 100% |
2 |
REQUIRED |
Minimum maintenance. | Annual preventive maintenance activities and other essential maintenance tasks:
|
95% - 100% |
3 |
MFR RECOMMENDED | Manufacturer’s recommended maintenance level. |
All OEM recommended PMs (weekly, monthly, quarterly and semiannually) |
85% - 95% |
4 |
TOP TIER |
Top tier maintenance activities. | All of the above items plus:
|