
Service: We focus our unconditional efforts to best serve our clients.
Part of the Values at Work Series
Facilities Team Finds Fix for Bellmont Hall Elevators AC Fail, Saves Texas Longhorns Football Season, Academic and Operational Access
Picture this: it’s a few weeks before the Texas Longhorns football team takes the field for the first home game of the 2022 season. It’s August, and the unyielding Texas heat lingers in the air, permeating the campus. Now imagine the air conditioning (AC) unit that serves the elevator control room at L. Theo Bellmont Hall (BEL) fails, which in turn causes the elevator systems there to automatically shut down as a heat safety measure.
Normally, it would just be a case of replacing the AC unit and then the problem would be solved. But this was a journey that took many twists and turns, testing the tenacity of our trouble-shooting skills. Fortunately for us, our team doesn’t give up easily; we stay focused to see our way through to resolution because we value providing the best service to our clients.

Failed AC unit at BEL
For the context of this story, it’s important to point out that BEL is an 11-story building that serves as a gateway to the stadium and its associated club and press boxes, as well as access for a multitude of academic and operational activities. The only acceptable option was to solve the problem at hand as quickly as possible. It was a critical issue at a critical time—the first home game of the season and the beginning of the fall semester. The scenario called for immediate and corrective action. Enter the facilities experts, where our ‘save the day’ story begins.
Getting the call
The Facilities Operations and Maintenance (FOM) division’s Zone 3 team serves East Campus and the Texas Memorial Stadium area, which includes BEL. They were notified by the elevator contractor that the control room on the 11th floor was getting hot. Upon investigation, Zone 3 technicians determined that the AC unit was no longer working and had to be replaced. They contacted an HVAC contractor, who said that it would take at least 26 weeks to get the appropriate replacement unit. That estimated time frame was simply not going to work. The elevators were needed in time for the first home game. The issue was then elevated to FOM’s Engineering and Technical Support (ETS) team to develop a faster, yet reliable, solution for bringing the elevator AC back online. Enter Jose Lopez, a maintenance engineer with ETS, who was assigned to manage the emergency project.
Trouble-shooting begins
It’s now August 22, and Lopez sets to work on the mission to quickly restore the AC to the elevators at BEL. He began the time-sensitive project by checking with other HVAC contractors, but the lead times were the same.
“At this point,” Lopez explains, “it had to be done in two weeks!”
There were no AC units to be had anywhere that met the specifications and would arrive within the needed time frame. Lopez concluded that replacing the AC unit in the specified size was not an immediate solution. It was time to look for a quicker, temporary way to solve the problem until the replacement AC unit would arrive. Or in the case of this story, ways to solve the problem due to the multiple challenges that cropped up during the course of completing the temporary fix. And as Lopez realized, he would need to collaborate with other facilities departments to make it all happen on time. Focus on our unconditional efforts was now fully engaged.
Temporary solution 1: Use spot coolers
The first idea was to place spot coolers in the space. Lopez explains that he contacted the HVAC contractor to discuss the option and any safety risks involved. He learned they would need six units, but there would not be enough power (electrical supply) in that space to support those units safely.
As Lopez relates, “Days are passing by. The pressure was on.”
But he would not be deterred. On to the next idea.
Temporary solution 2: Install a rental AC unit
The second idea was to install a rental unit. The specified size was not available to rent, but Lopez was able to identify an HVAC rental contractor who had a larger AC unit that could fit in a mechanical room area on the same floor as the elevator control room. This area also contained a 480-volt electrical panel that could be used to power a larger unit. Problem solved! Well, not just yet. There were a number of obstacles the team would still need to overcome to complete their mission. We won’t let these obstacles stop us.
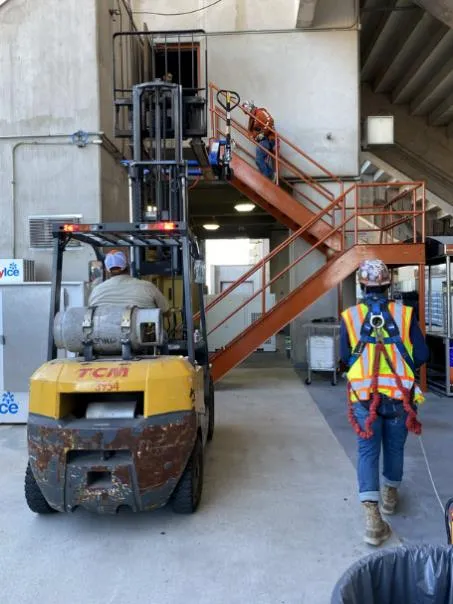
Staircase and guardrail to mechanical room on 11th floor of BEL.
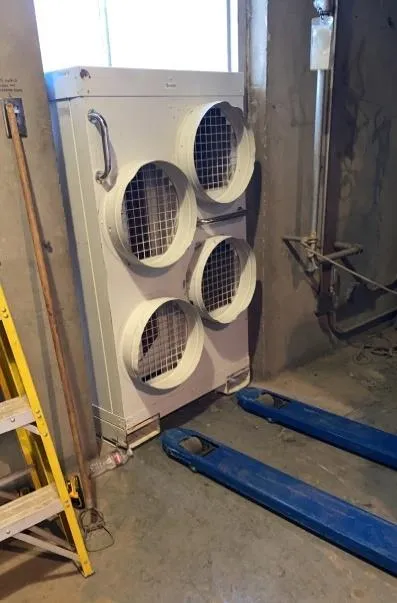
Bringing the rental AC unit through the door using a pallet jack.
Obstacles to Overcome
How to get the larger rental AC unit up to the space. According to Lopez, “We needed a way to move the 1,300-lb. unit up to the 11th floor.”
He contacted the director of Athletics’ Maintenance & Operations, Mike Rodriguez, for help because they have forklifts in the stadium. But he didn’t have an operator for the forklift available because they were very involved in getting the stadium prepped for the upcoming game. Thankfully, that’s where Juan “John” Uballe, an electrician with Zone 3, came in. Fortunately, he was already forklift certified.
“We were able to borrow the forklift from Mike, and John could use it to bring the unit up to the 11th floor using the ramp from inside the stadium” said Lopez.
The plan was to then forklift the unit up to the slab in front of the door, then use a pallet jack to bring it into the space through the door. The plan was great, only the execution came with more challenges. We’ll figure this out.
A guardrail was blocking access to the door. “We had to have a contractor cut the guardrail before we could forklift it up. Then immediately weld the guardrail back after the unit was in place. Facilities Services’ safety manager oversaw this part of the operation, ensuring that the proper personal protective equipment, such as a safety harness for fall protection, was used appropriately.”
What was the next obstacle to face? We can do this!
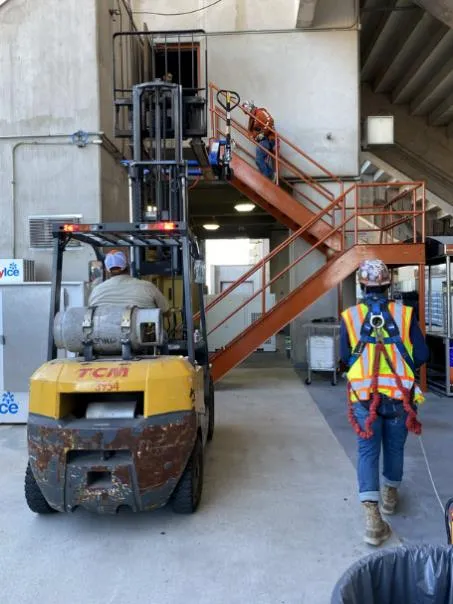
Removing the guardrail and testing the forklift with safety in mind.
Getting the unit through the door into the mechanical room. It was a tight squeeze.
“We only had a 1” clearance to get the unit through the door,” explains Lopez, who operated the pallet jack to move the unit into the room from inside. Now on to the next challenge.
The rental AC unit had to be tied in to the existing ductwork of the old unit. This was one of those times when collaborating with another facilities department was essential for completing the project on time. The Sheet Metal Shop with Construction Services pitched in with custom-made collars (ductwork connectors) and insulated ducts that would enable the new unit to tie into the existing ductwork. Ken Smith, a sheet metal technician, installed the custom ductwork, overseen by Lopez. Stay focused; we’re getting closer.
Connecting insulated ductwork into existing ducts.
The 480-volt electrical panel in the mechanical room space did not have a spare 50-amp breaker, which is what the rental AC unit needed to power it. Our Zone 3 electrician, Uballe, was brought in to help secure the required breaker. First, he had to source the breaker because he didn’t have one in Zone 3. He checked with the other zones, but they didn’t have one either. He then called an engineering contractor to see if they had one in stock. And they did! Things are looking good now. Until they ran into another snafu. Not a problem; we’ll solve this anyway.
We still need the breaker. When the contractor went to pick up the needed breaker at their facility, it wasn’t there. It was out of stock after all. Uballe searched other UT buildings to see if there were any spare 50-amp breakers in other electrical panels, but he didn’t find one. Okay, let’s come up with another solution.
Could the contractor find another 50- or 60-amp breaker? In the meantime, John was looking for a 60-amp breaker in another building.
Lopez explains, “All this was happening the day before the scheduled install of the temporary AC unit. Using the 60-amp breaker would work with a 50-amp breaker disconnect (a separate box outside the panel). But we needed the 60-amp breaker.”
Meanwhile, the contractor was still outsourcing to assist with the search. Lopez and the team finally get a call from the contractor that they found a 50-amp breaker!! It was overnighted to their local operations, and it arrived the next morning. One of their local technicians came to campus with the new breaker and installed it.
According to Lopez, “the breaker arrives about 5 minutes after we had placed the rental unit in the space.”
Talk about timing. Now on to the moment of truth.
The seeds of success were planted
Would all the trouble-shooting lead to victory? Lopez and the project team had put in every effort to complete the project on time. It was time to put their efforts to the test. The unit was turned on, and everything worked fine! Success at last!
Scott Griffin, Facilities Services’ interim director, sums up the way this time-sensitive project unfolded, “This fantastic effort epitomizes what we strive to achieve every day: taking care of our customers! It is inspiring to see a team coalesce around a challenging problem, develop a plan of action, and execute it to perfection. Job well done.”
For media inquiries, contact Valerie Nies at valerie.nies@austin.utexas.edu or by cellphone at 512-627-7577.