The advent of direct digital controls (DDC) has propelled the technology, capability, and complexity of building operations forward over the last 15 years. The combination of DDC and intelligent operating systems combine to create a Building Automation System (BAS). A BAS centralizes the control of a building’s heating, ventilation and air conditioning (HVAC), lighting, and other systems. “Intelligent” buildings improve occupant comfort, provide efficient operation of the building systems, and reduce energy consumption and operating costs.
“Building Automation Systems are much more complicated and technical than earlier control systems and require technically savvy employees to maintain and operate them.”
However, they are much more complicated and than earlier control systems and require a new generation of employees who are computer literate and technically savvy to maintain and operate them. At The University of Texas at Austin campus BASs are operated and managed by the technical specialists from the Building Operations group led by Mark White, Building Operations manager. The group is a branch of the Facilities Operations & Maintenance (FOM) division of the university’s Facilities Services department. They are responsible for programming, monitoring, and analyzing the campus building systems. White knows better than anyone how complex these systems are and set out to ensure our BAS operators and instrumentation and controls (I & C) technicians are proficient at diagnosing, troubleshooting, and repairing these systems. With more and more buildings coming online, and the number of intelligent buildings increasing with the transition from pneumatic to digital controls, White needed a hands‐on training method that would give technicians the field experience they need without affecting the real systems or building occupants. The solution was to design two training and simulator devices. At first glance, you will wonder whether you are in a jetliner cockpit or perhaps a control tower. But you are in a warehouse‐turned‐office space at The University of Texas at Austin’s Facilities Complex—the new home for two large, highly technical simulators that serve as training and testing devices for the university’s Facilities Operations & Maintenance staff. The simulators provide technicians with hands‐on experience on our two primary BASs: Andover Continuum and Siemens Apogee. The two training benches are comprised of a BAS workstation and several BAS controllers and hardware components common to the BAS systems used on our campus. The benches also include an interactive air handler simulator panel to mimic the operation of an actual air handler unit in the field. Since the benches were designed to be mobile and self‐contained, they can be used in conference and training rooms for larger groups. White anticipates that the benches will help develop the ability of staff to use the operating systems software, diagnose and troubleshoot BAS components and field devices, and test control programming and system hardware.
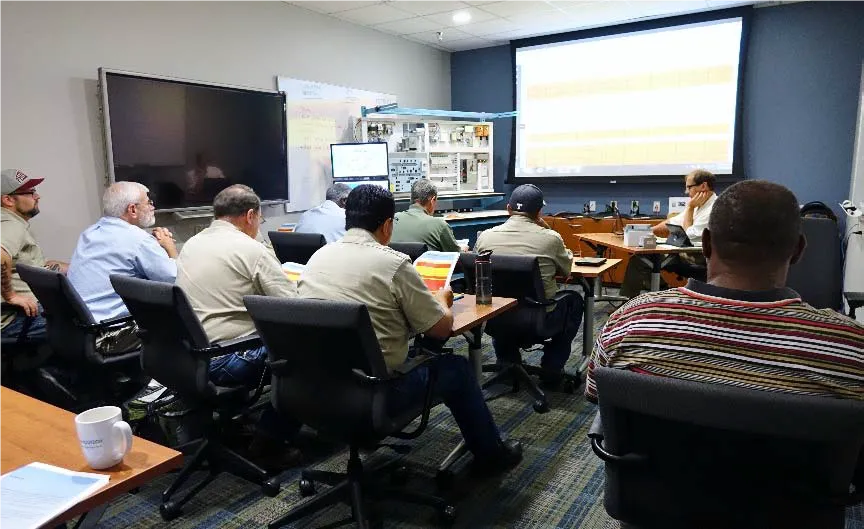
Technicians attend in‐house course using training bench
The simulators are incorporated into courses developed as part of the FOM division’s in‐house training system, which provides more efficient use of the university’s resources. White began administering the courses using the training benches in early August 2015. As he points out, “We’ve trained 48 technicians to date and provided additional one‐on‐one coaching sessions. More classes are in development. The feedback from the first few classes has been excellent, with an average survey score of 34 out of 35 (96 percent positive).” “We can also talk about the economics of the in‐house training system,” White says. “It costs approximately $3,000 per person, including travel, to send technicians to off‐site manufacturers’ weeklong training. We’ve trained over 50 people so far. By using a train‐the‐trainer concept, the benches have already saved more than $12,000 in avoided tuition costs—and more when factoring in avoided travel costs. Given our limited budget for training, it would have taken 3‐5 years to send that many people to an off‐site class, and many of them would probably not have had the opportunity to attend at all. We now also have the capability to retrain and reinforce what they learn anytime we want.” Building operations at the university have evolved as the technology that drives them has evolved into the digital age. The technicians who keep these complex systems running must now possess more technically advanced skills and knowledge. The university’s Building Operations group has risen to the challenge through innovative solutions such as the training benches. As President Fenves took office, he spoke of his commitment to pursuing excellence in innovative ways, and we in Facilities Services stand behind that commitment.
"We’ve trained over 50 people so far. By using a train‐the‐trainer concept, the benches have already saved over $12,000 in avoided tuition costs— and more when factoring in avoided travel costs.”
“We are really excited to have these two benches as a training tool for our staff,” White says. “If you have any ideas on training opportunities where these systems might be used, please don’t hesitate to contact me.”For more information or to see a demonstration, contact Mark White at 512‐232‐1953 or at mark.white@austin.utexas.edu.