
Stewardship: We conduct our business in a manner that is reflective and protective of the public trust in us as stewards of the University’s facilities.
Part of the Values at Work Series
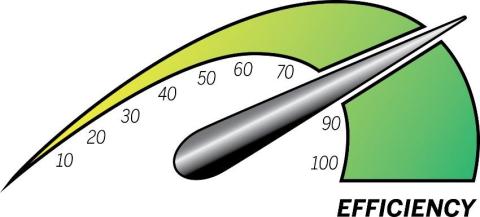
After facilities managers address their client’s unplanned maintenance issues, provide the necessary preventive maintenance on building systems and manage energy conservation efforts, how do they also find a way to optimize the performance of the buildings on campus so the systems run as well as they ought to…and do it all with limited resources? Building Operations Manager Mark White provides insights into how The University of Texas at Austin, with the help of its Building Optimization Team (BOT), is moving the needle toward impactful facilities optimization on a university campus.
What is the BOT?
The Building Optimization Team (BOT) is a group of technical specialists within the Facilities Operations & Maintenance (FOM) division of the Facilities Services department at The University of Texas at Austin (UT Austin). The BOT implements a technical process that improves how existing building equipment and systems function together. They target buildings that are good candidates for improved performance and conduct in-depth assessment of systems in those buildings to identify deficiencies that negatively impact efficiency. They also address those deficiencies themselves or coordinate the work with other sources. As a result of these efforts, the targeted underperforming facilities operate more efficiently, or as intended, which provides multiple benefits to both the building occupants and the university.
This article explores the BOT program in more detail, including its history, expertise, methodology and benefit to the institution. Of distinct importance is the heightened level of collaboration employed by these specialists. Not only do BOT members possess strong technical knowledge and skills, but they also have developed ways to increase communication among the diverse parties involved in their projects, which has helped build cooperation and improved project outcomes.
History at UT
The BOT was organized in April 2012 in response to sustainability initiatives set forth by the university’s leadership, where an energy conservation goal to cut consumption by 20 percent by the year 2020 required more efficient building operations in order to help meet the goal. Facilities managers at the university believed the key to making the buildings more efficient was to assemble a team of dedicated resources that would be able to focus primarily on improving the overall building performance, which would then yield multiple benefits even beyond a reduction in energy usage. But where would the team come from? Who would best fit the role?
In the past, instrumentation and controls (I&C) technicians at UT Austin handled building performance issues, but their efforts were driven more by responding to customer calls and making repairs than by providing long-term, holistic solutions. FOM management considered their resource options. We need to create our own program, and it will need to be internally sourced. What if we pulled our I&C crew leaders from the various zone maintenance shops and re-focused their efforts on optimizing our buildings? And so the Building Optimization Team concept evolved. But it would take more than just bringing a team of senior-level technicians together. Beyond a new group name, the members of BOT needed a new perspective. They also needed more training to enhance the skills and knowledge they already had.
What expertise and qualities are needed?
![]() UT Austin's Building Optimization Team (from left) Kurt Kern (supervisor), Kevin Preuss, Mark White (manager), Roger Hale, Dale Ritterbusch, Randy Ford. Not pictured: Ron Cooley, David Holub. |
To build an effective BOT, members must have excellent diagnostic skills to troubleshoot system issues, such as functional testing of sequence of operations on building systems, and they need to know the correct way to measure and verify building systems.
UT Austin’s BOT has a combined 126 years of technical skills applicable to instrumentation and controls (I&C) and building optimization. Together, they have extensive training in controls, motor controls and starters, electrical, high-voltage safety, water heaters, variable frequency drives, pumps and steam traps, as well as the testing, adjusting and balancing certification on the systems installed at the university. Many have earned their Certified Control Systems Technician® (CCST®) designation through the International Society of Automation (www.isa.org), the industry standard for building automation professionals.
There are also members who hold degrees in related areas such as electronic technology and computer engineering technology.
Just as important as their technical skills is their ability to look at the systems holistically and not just by the individual components. An integral part of operational efficiency is how well the building components work together.
They need to understand that they must approach each building differently. Each facility has a unique set of conditions that affect how it functions. Therefore, the right solution for one building may not be right for another. For example, an office building has different operating requirements than that of a research laboratory required to maintain specific environmental conditions, such as the consistent and reliable removal of hazardous chemicals from the air where scientists work.
They need to associate a building’s usage with the occupants’ mission and the university’s mission. Overall, a good working knowledge of the institution helps them to know the facilities first hand and to build trusting relationships with building managers and occupants. In many ways, they become like campus “doctors” whose “patients” are the university’s facilities.
“We’ve had to rethink the way we do things,” said White. “What’s the best solution, not just any solution. We have to be thoughtful, and not just do what’s easy.”
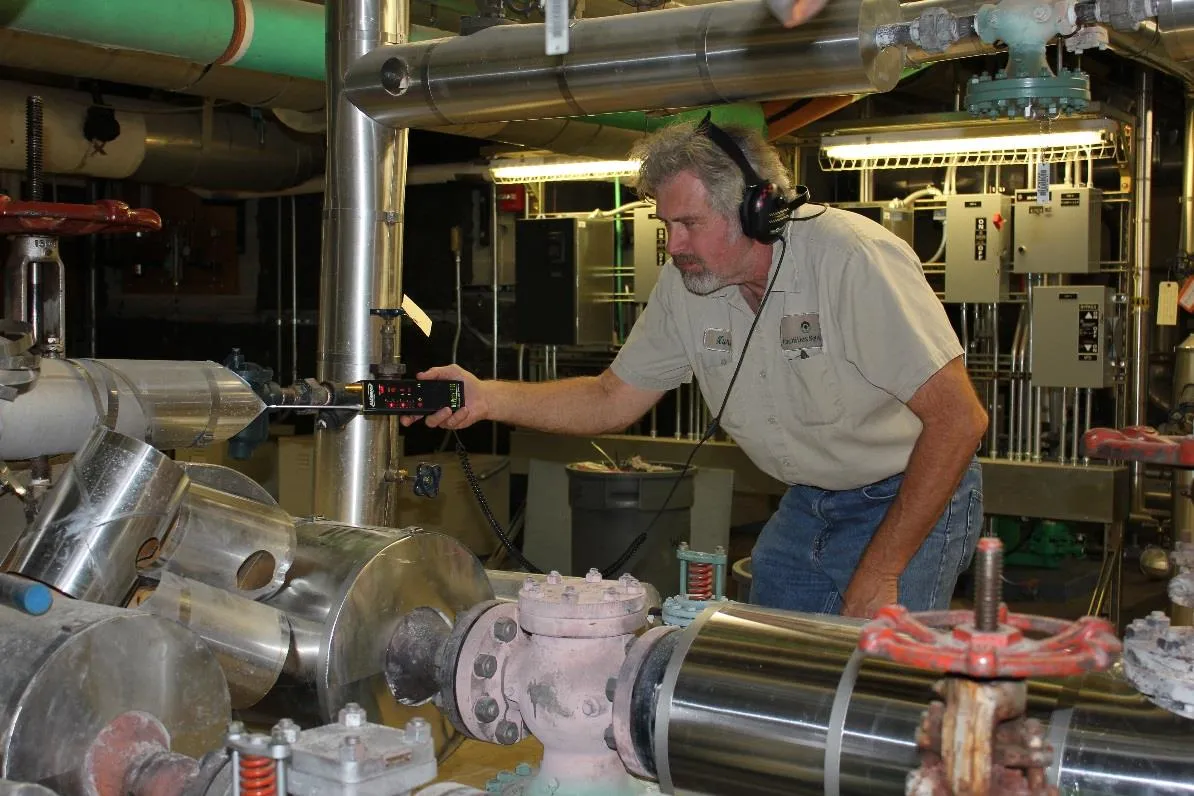
Technical inspections are part of the building optimization process.
Building Optimization Process
In general terms, the process begins with a technical inspection that takes place after a building has been completed and occupied. Technicians measure and verify how existing building equipment and systems are
operating in the facility. The audit provides data the technical team can use to identify issues that should be addressed in order to improve building operation. Addressing the issues improves how existing building equipment and systems function together.
Selecting a Building
BOT members selectively identify buildings for potential auditing and retro-commissioning (described below): those with energy usage issues such as high consumption, or known environmental problems such as occupant discomfort. From among buildings determined to have energy challenges, the team further narrows the field by identifying those in which they can likely have a positive impact and excluding buildings where upcoming projects will take place. This evaluation process occurs bi-annually in collaboration with stakeholders, including the university’s Zone Maintenance and Energy and Water Conservation (EWC) units.
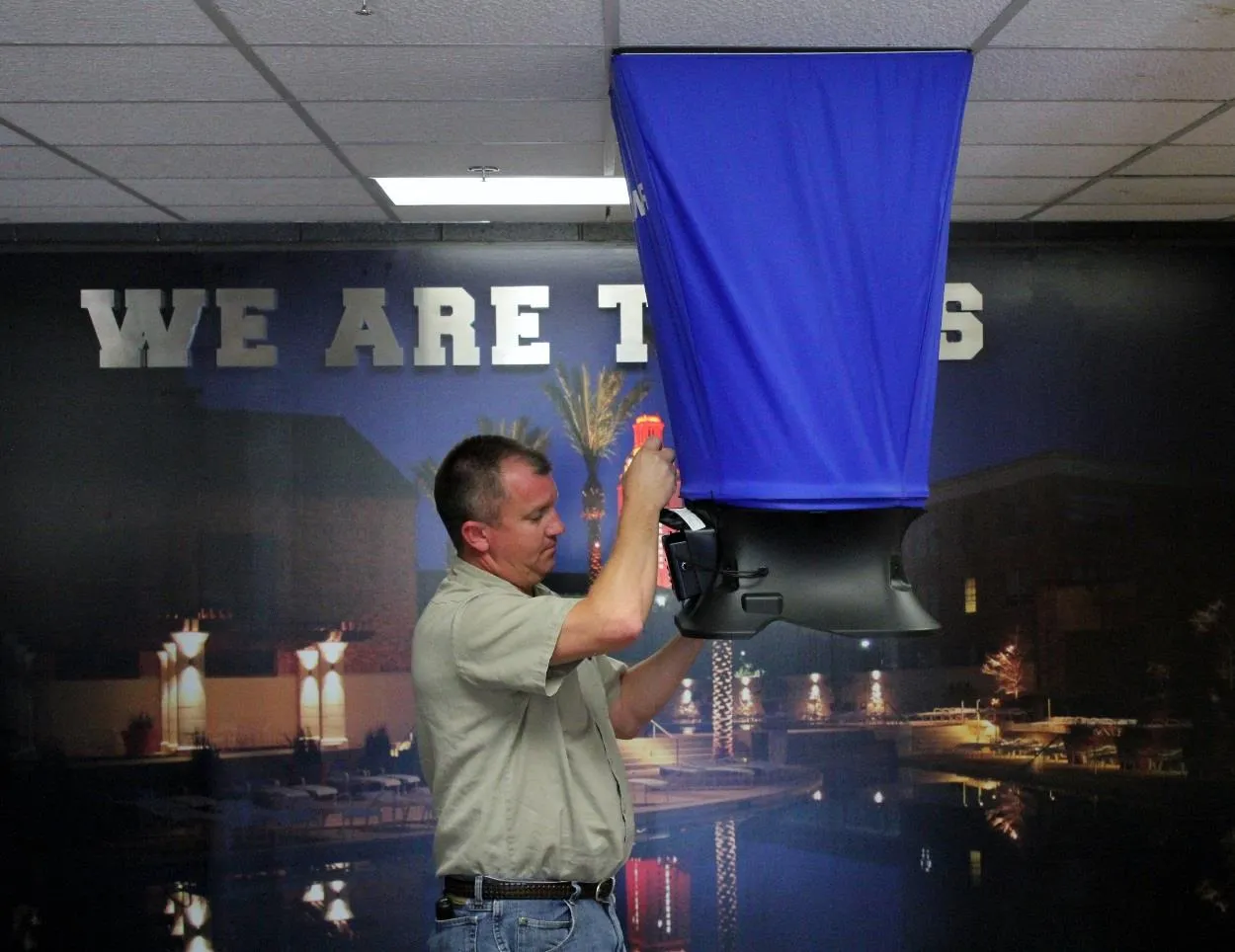
BOT technician performing audit of building systems.
Auditing Building Systems
Once the BOT selects a building, they audit it by closely following desktop instructions developed by the team, “Building Optimization Process Inspection Best Practices.” These instructions cover 17 building systems--from air handling units to chilled water, steam, fans and more--detailing the measurements to be taken and verifications to be made. For example, steps for auditing a process chilled water (PCHW) system include
visually inspecting the system; comparing the actual PCHW pump differential pressure with the building automation system (BAS); comparing the actual supply and return water temperature with the BAS and verifying that the system is controlling to set point; comparing the variable frequency drive (VFD) speed with the BAS and comparing VFD feedback to the BAS and the speed command. Steps also include comparing the valve position with the BAS, verifying the valve operation, and verifying that the valve fails to the correct position. Although complex, the PCHW audit actually has many fewer steps than most of the other 16 systems inspected!
Retro-Commissioning
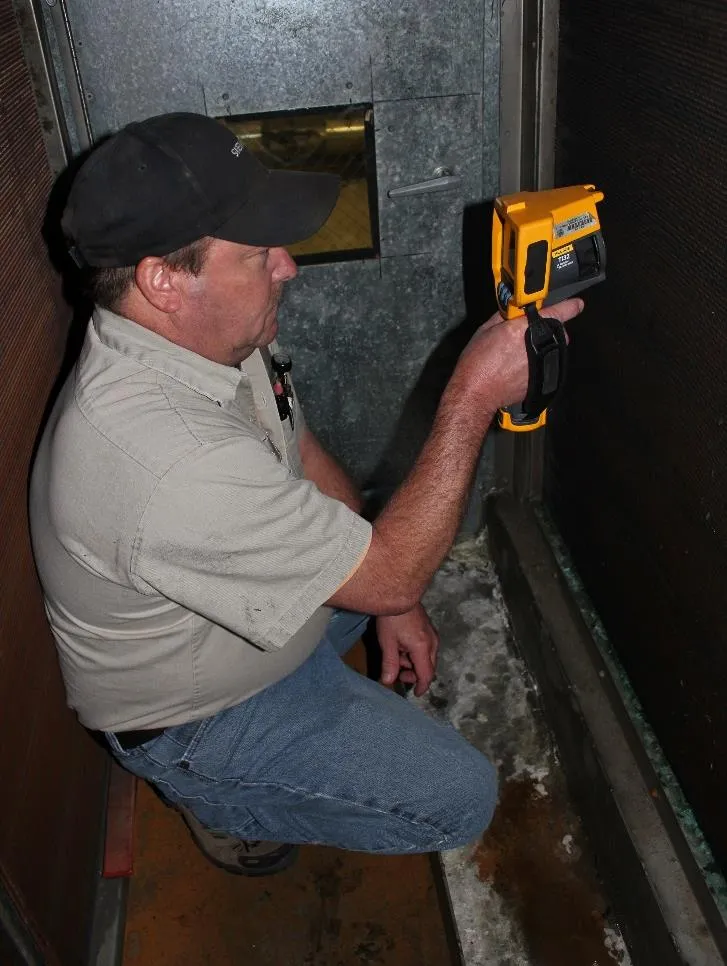
Testing, measuring and verifying data is integral to the BOT process.
Using results as a guide, BOT members create a work repair plan for the audited building that identifies what needs to be done and who will do it. The work repair plan evolves as the team tests, measures, and verifies BAS data, and it notes problems to be assigned to deferred maintenance as appropriate.
“The work repair plan is not linear,” said White. “Testing, measuring, verifying and updating the plan can all be going on at the same time.”
Role of Technology
The BOT relies on technology to establish baselines, as well as to support the repair plan and the actual work. In addition to various instruments for testing air, water balance, and other indicators of building system function, the team uses an auditing application for building optimization developed in-house. The app provides a way for team members to record measurements and test results electronically and store them in a centralized database. “This paperless process replaces spreadsheets, eliminating the need to transpose information and reducing the chance of errors during input,” White explained.
The team also takes photographs and uses Visio to develop baseline drawings of systems. These are also stored centrally.
Providing Additional Building Improvements
Beyond bringing buildings into operation as they were designed, BOT members may provide additional building improvements such as tightening temperature controls, stabilizing humidity controls, and installing upgrades to existing control systems, especially when they can achieve a substantial positive impact on the building’s performance. BOT members may also perform or coordinate any needed repairs in-house. That’s one reason why White describes UT Austin’s BOT process as “retro-commissioning on steroids.”
BOT Outcomes and Benefits
BOT members perform their retro-commissioning process to get the equipment to operate as close to the original design (as intended) or to improve its operation in the space. Their process may also include correcting mechanical issues that can only be found during the in-depth testing, measuring and verification that occurs with this process. Examples include checking the air flow, space temperatures and indoor air quality.
As a result, BOT members bring to the facility improvements in occupant comfort, indoor air quality, and health and safety. For example, in one building they found and repaired carbon dioxide (CO2) sensors that were not functioning properly and thereby causing excessive outside air to be utilized, resulting in higher-than-normal energy costs.
Energy Conservation
Energy conservation was a strong incentive for developing the BOT, as the group plays a role in helping the university to meets its conservation goals. The team looks at and, as needed, addresses chilled water, steam, HVAC and electrical systems.
The chart below (Chart 1) shows measured values in blue and, in red, the expected baseline at the Peter O’Donnell Jr. Building (POB), had BOT not been involved. The difference between the two lines represents avoided electricity consumed, averaging to 30,152 kWh/1,658/103 MMBTU per month.
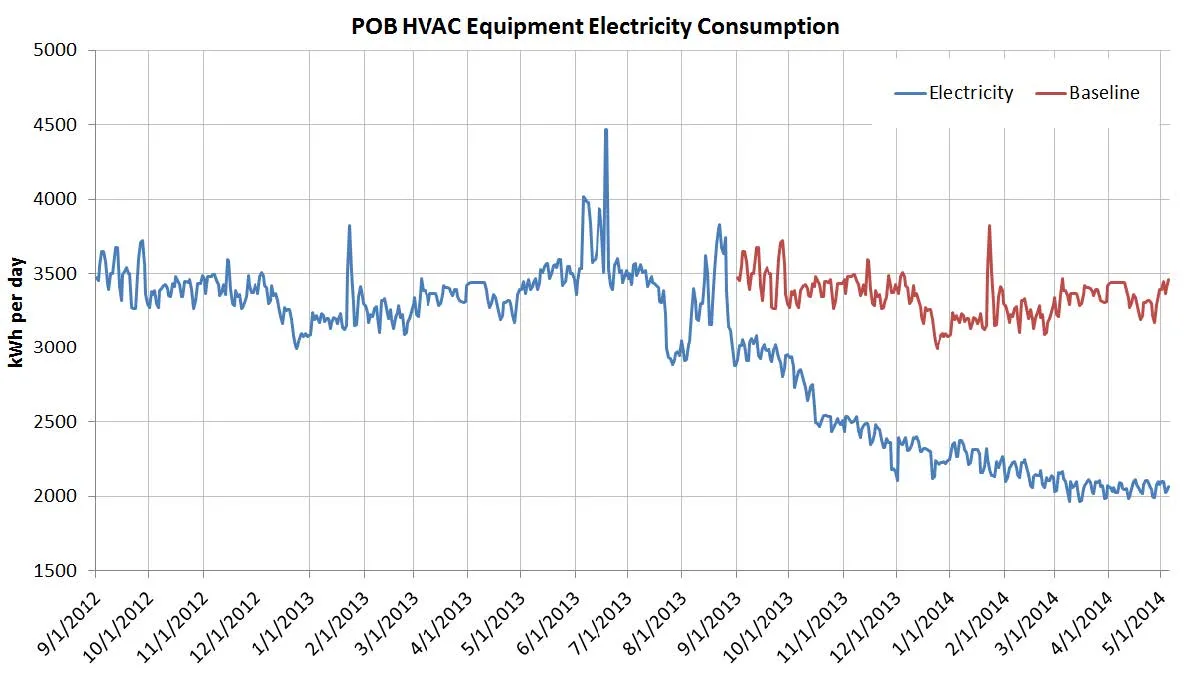
Chart 1: Energy Reduction (Electricity) at the Peter O’Donnell Jr. Building (POB)
The chart below (Chart 2) shows reduced consumption at POB during the winter and surrounding months, with calculated consumption decreasing as the weather warmed into May. The average reduced consumption over the winter and surrounding months has averaged 42,102 ton-hrs./7,157/505 MMBTUs per month.
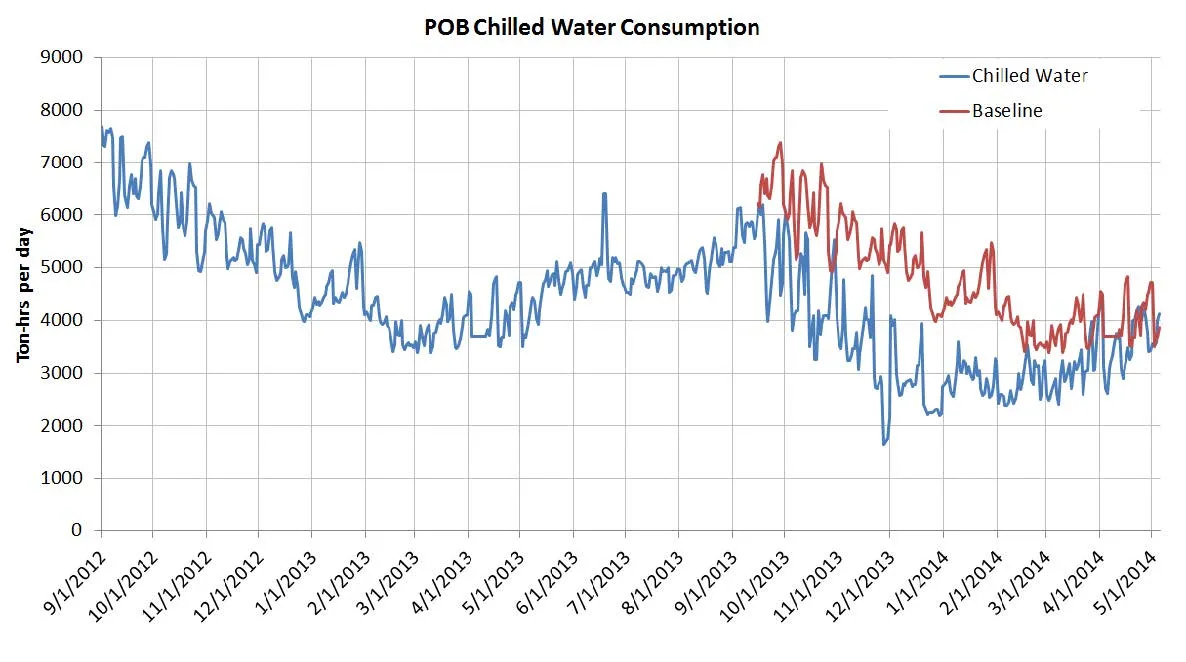
Chart 2: Energy Reduction (Chilled Water) at the Peter O’Donnell Jr. Building (POB)
Proactive Process
Overall, BOT applies a proactive process that greatly reduces the risk of potential down time on building systems normally associated with responding on a more reactive basis. Further, employing a proactive process helps to reduce labor hours. When a building is operating properly, the number of client calls for hot and cold issues is decreased. Finally, the process highlights the extent of deferred maintenance needed on campus. The chart below (Chart 3) shows a comparison of the total number of annual hot/cold calls received prior to and after the re-commissioning process was completed at POB. The number of hot/cold calls received was reduced by 32 percent as a result of the project.
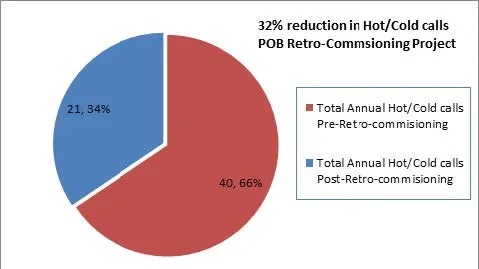
Chart 3: Reduction in Hot/Cold Calls at POB.
Communication Is Key
Communication is critical throughout the auditing and retro-commissioning process, as team members share building information, schedules and impacts among the team and with key building contacts. Toward the close of each day, team members who are auditing must upload their data to the app, and a team member sends an email to other BOT members describing results of the day’s work. The summary email assists with planning the next day’s work, including ordering any necessary equipment.
While at work in a selected building, the team reaches out to the building operator at least daily. The team sends a weekly summary to building managers, zone shops, and EWC; these summaries become a cumulative, single document for ongoing reference. Every other week, BOT members lead an Optimization Shop meeting to share updates and discuss issues with FOM managers, zone supervisors, and EWC stewards.
Based on the unique needs of each building, the team may reach out to Zone Maintenance or other FOM unit, or EWC or other Utilities and Energy Management (UEM) group to gather or share information. In coordination with the building manager, the team may even communicate directly with users of the spaces.
Reporting Back to Clients
Once their work in a building is complete, the BOT publishes a commissioning report for the client.
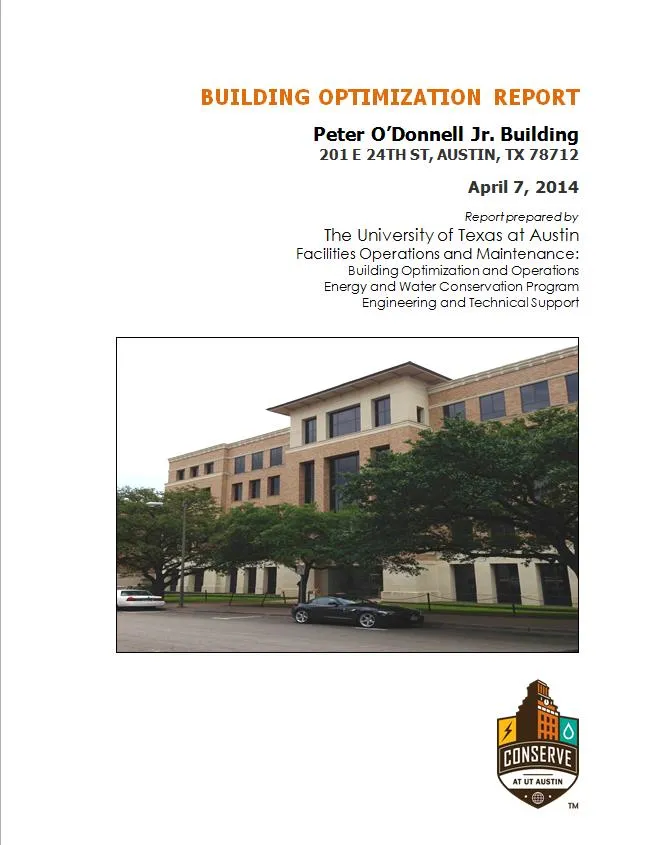
Commissioning Report for Peter O'Donnell Jr. Building
Each report includes the scope of work—what was done and expected impacts. In addition to providing documentation for the building client, the commissioning report documents the process and results as a reference for all FOM staff. BOT and Zone Maintenance use the report for debriefing, in order to improve the work that they do.
The entire audit and retro-commissioning process has been fine-tuned over time, according to White. “The process is tweaked with each building,” he said. “We can adjust the process for each building more quickly now, due to practice and the debriefings.”
Feedback from Clients
As stated earlier in this article, the BOT provides a report to their clients with the information and data on the measured corrections and improvements for the buildings involved in the retro-commissioning process. But one of the most important measures for the success of the BOT’s projects is the level of client satisfaction. Clients have provided feedback about the retro-commissioning process they experienced, such as these statements:
“We have experienced a lot less complaints with regard to areas being hot/cold and the overall temperature of the building is much more comfortable. Your team did an excellent job with communicating, responding to problems as they arose and fixing any problems that arose. I think the overall outcome of the Building Optimization Team going through our building has made very positive changes for our building in the future.”
Annette Noorzad, Business Manager ACES IT Group Office of the Vice President for Research Peter O’Donnell Jr. Building (POB)
“Overall I’d say my experience with the BOT work in WEL was pleasant and productive. I did appreciate the effort to communicate what was happening, especially the planned shut downs and the weekly summary.”
Steven Moore Assistant Director, Facilities & Safety Chemistry Department Robert A. Welch Hall (WEL)

“I would like to compliment the Building Optimization Team (BOT) on their professional and dedicated approach to analyzing the problems with the HVAC system in MBB. I attended their kick-off meeting and was reassured that there would be constant feedback and communication all through the project. This was very much a consistent feature of their management and coordination style. Suffice it to say, that I am extremely pleased with their work and the final result, with the building HVAC operating in accordance with design criteria.
Moffett Molecular Biology Building (MBB)
Robin Newton Facility Manager College of Natural Sciences Moffett Molecular Biology Bldg. (MBB)
“The Building Optimization Shop recently conducted a comprehensive audit of our building’s HVAC systems. . . .
Before the audit, we had started noticing that the HVAC system was not keeping up with demand in several areas. . . .
Mark and his team started at the air handler unit level, and worked their way down to individual room control damper motors. This task required a high level of technical knowledge and building familiarity. . .
This audit was responsible for finding over 180 deficiencies in our HVAC infrastructure, including high impact malfunctions such as supply fans having the reverse rotation. Once those repairs were made, we noticed a dramatic improvement in the quality of air . . . .
Building zones are able to maintain a much tighter temperature range, which helps ensure research consistency. . . .
The fact that a large number of deficiencies were discovered speaks not only to the critical need for such projects, but also the effectiveness of the BOT team. . . .
I’d highly recommend this audit to other building managers across campus, it is well worth the effort.“
Nachiketa Shukla
Building Manager/Facilities Manager
Animal Resources Center (ARC), Vice-President for Research
Summary The Building Optimization Team at The University of Texas at Austin implements a technical process that improves how existing building equipment and systems function together. In their targeted approach and in-depth assessments of systems, they identify and address or coordinate the correction of deficiencies that result in multiple benefits to the facilities and their stakeholders, which can include:
- Reduced energy consumption
- Improved building performance
- Improved comfort levels for building occupants
- Reduced maintenance costs
- Extended equipment life (in some cases)
White’s team has built a methodology for optimizing building performance at the university and continues to fine-tune its efforts. The BOT is moving the needle toward efficient and effective facilities operations on campus, but not without looking very closely at the needle to ensure it is operating as it should.
For more detailed information or inquiries, contact Mark White at mark.white@austin.utexas.edu.
Read more about the Building Optimization Team at The University of Texas at Austin.